Alutronic saves 20% gas in anodizing operation
Optimization in gas consumption implemented
"We've always done it this way" is generally considered a development blocker. But in the case of our complex anodizing process, the sentence did carry some weight. Now the upcoming modernization of the heating system came together with the enormously increasing energy costs and supply risks. We decided to test a process that had been in place for 30 years. The test was successful and our CO2 emissions will benefit in the future from a saving in gas consumption of at least 20%. The price increase can thus also be reduced somewhat.
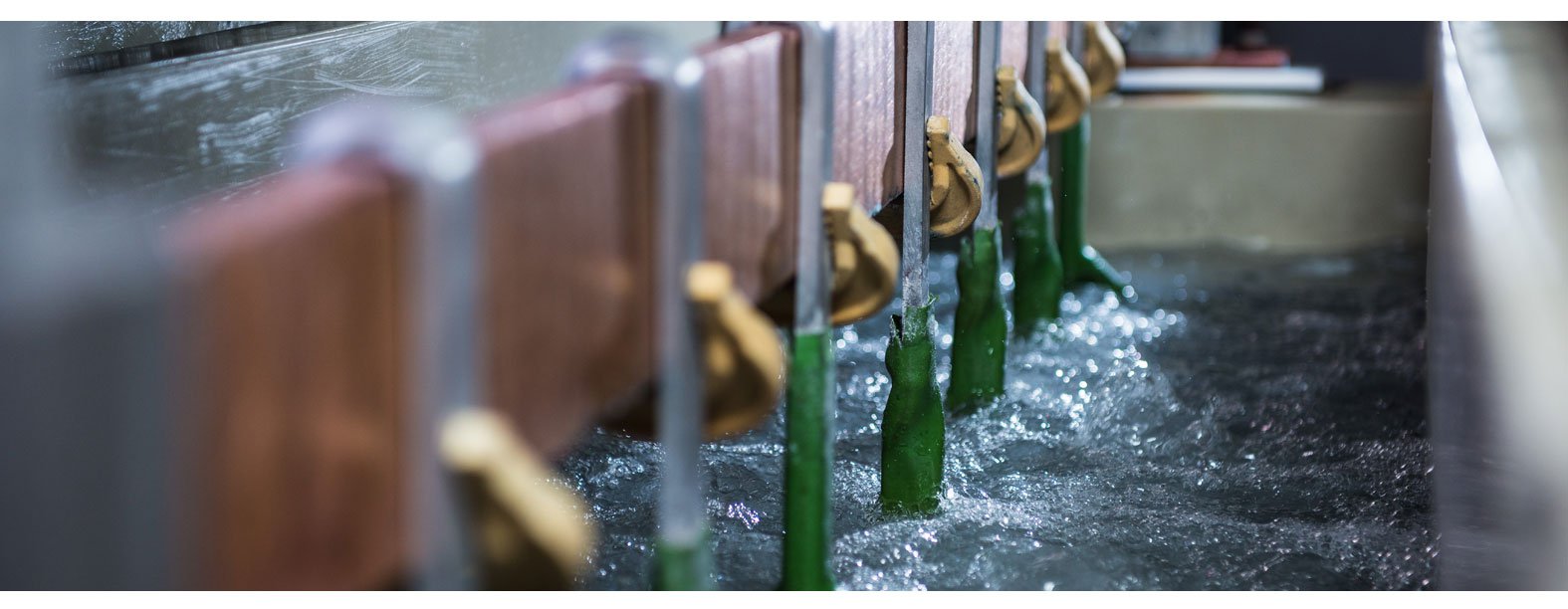
With an average consumption of 300 MWh/a in the anodizing plant, the savings potential would thus be in the range of 60 MWh/a.
The following possibilities and measures have been initiated or can be integrated (for the technically interested):
1) The supply temperature of the boiler system is reduced from 99° C to 75 °C. The baths with a heat demand of 99° C are reheated electrically with immersion heaters ( 35kWe). The process has been tested and the immersion heaters are already in operation. Other baths are being converted. The heaters are/will be integrated into the control system to compensate for the missing power.
2) Converting process baths to lower temperatures during operation.
3) Closer adjustment of the times in relation to the transitions= rest/production,
Reduction of process temperature, closer synchronization working time / plant readiness.
4) Sequence adjustments production times and rest times to extend the
rest times
5) Extension of dynamic bath control with MV technology
We are happy to share our knowledge in this area. Please contact our Mr. Thomas Lauff lauff@alutronic.de